
Pre-Cut vs. Post-Cut Roll Forming: Which is Right for Your Operation?
Meet the Panelists
Watch the Video
Listen to the Podcast
Read the Transcript

We Want Your Feedback
We’d love to hear what you think about Formtek Talks so we can make these better as we go along. Even feedback about what topics you’d like to see us tackle in future episodes would be great.
Meet the Panelists

Brian Kopack
Vice President of Sales | Formtek, Inc.
- 22 years in the metal forming and manufacturing industry
- Bachelor of Science Degree | Mechanical Engineering from Case Western Reserve University

Paul Williams
Vice President of Business Development | Formtek, Inc.
- 38 years in the metal forming and manufacturing industry
- Former Chairman, Trainer, Speaker for the Roll Forming Council of Fabricators & Manufacturers Association, Int’l (FMA)
- Bachelor of Science Degree | Business Administration from Kennedy Western University

Darren Muchnicki
President | Formtek, Inc. and Mestek Machinery, Inc.
- 20 years in the metal forming and manufacturing industry
- Bachelor of Science Degree | Mechanical Engineering from Kent State University
- Leadership Deep Dive – Executive Education from Weatherhead School of Management at Case Western Reserve University
Watch the Video
Listen to the Podcast
Read the Transcript
All right. Welcome to Formtek’s podcast on pre-cut versus post cut. This is a common question that we received quite often through our customers and talking to… Either through quotes or at trade shows. Before we get going, I’d like to first define what it is that we mean by pre-cut versus post cut. Pre-cut we’re feeding a roll former a pre-cut blank that has a specific length. Post cut, we’re essentially cutting the length after we roll form the part.
And we’re going to show the two types of lines for our listeners to the podcast. If you want to look at our YouTube video, you can pick that up later, but basically we’re going to show you the two different diagrams. Now there’s a few versions of how these lines can be arranged, but generically speaking, a pre-cut line, you’re going to have either hand-fed blanks or you have an uncoiler with a pre-cut type of device, either a press or some other device that is cutting the strips, feeding it into the roll former.
Pre-Cut Operation
With a post cut line we have an uncoiler that we’re feeding off a coil into the roll former, and then we’re cutting with a specific type of press after we roll form. So the big question here, that we often get, and I’m going to start with Paul on my left and I have Darren on my right. I’m going to start with Paul, that one of the big things we get is, “Which one do I use?” Why would one company want to consider one versus the other?
Post-Cut Operation
Well, usually in the roll former if you’re running pre-cut, you end up having more forming stations, right? It’s usually… The rule of thumb is 25% more forming stations than if you would run from coil. And that’s because as you form the part, you can’t move it as quickly and it will want to open as it goes into each station. So it takes more of it to take a set, to minimize flare. The other side of it, what Paul alluded to, is part length. If you have long parts, it’s not a question. But it really comes down to what about… What’s your shortest part is the issue. Longer parts, you just need more space on the front end, the smallest part you have to be in two driven stands at any given time. So like Paul said, three horizontal centers of your machine is usually the minimum requirement.
Are there ways around them? Sure. There’s creative ways you can do. You can make tab parts so that you can run… Essentially run a longer part through, break it off, and then you get the two parts that you need. There are tricks that you can do, but in general, most people can’t live with that. Because you’ll have little dimples on the end, right? If you tabbed it. But some people can. It just depends on the application. And also the other thing that determines pre-cut versus post-cut, and I think Paul will probably touch a little more on it, is can you even cut the part off in a reasonable way without adding a bunch of pre-notching or other things? So your part itself may dictate pre-cut versus post-cut. For example, if you look at-
Flare

Yeah. I can think of refrigeration, mullions, some office products, partitions, things like that. Ball-bearing drawer slides, while a lot of them are small, there are longer ones you’d never want to go ahead and try to do a pre-cut and stuff like that. But another thing too, that comes to mind is that anytime we’re pre-cutting or post cutting and we have any punching, depending on the amount of stand, if the roll tooling is not designed correctly, or we don’t have enough stands, or the type of machine is selected incorrectly, can affect the type of notches and things like that, features in the product.
We did see like in an office partition where typically the tolerance… They go from 12 inches to 84 inches, let’s say, and the first to last slot has to be plus or minus 15 to the total, okay. It’s not cumulative. We did see with enough passes where we had a 32 pass mill with a welded system at the back end, where we saw no stretch because we had so many passes they were repurposing a mill. So, while that isn’t typically cost-effective to throw in a whole ‘nother roll former or doubling the amount of passes-
Yep. So there’s a couple of things to that. So it comes down to, usually with the roll forming process, we want to have it continuous, we don’t want to start-stop even with a post-cut system, right? We can do that and we can do simple one inch cuts or anything like that. But once again, it comes down to the throughput. Just because the roll mill speed can do something, you have to speed up, slow down, stop and cut. So we’re always looking to try to do something that is continuous and on the fly. So it comes down to line speed and minimum part. So in general, when somebody asks me that I say, “Well, easily, I know I can do a 36 inch part at 150 feet a minute.” And some of it’s… The calculations are linear, then. So 18 at 75, okay?
You have nine at 38 yield type of thing. And I back up just quickly, if somebody asks me that off the top of my head, then it comes in the type of die, depending on what we have to do, okay? And the stroke of the press. And that comes into play of my cycle time of presses and what kind of measuring system. And so there’s other things that come along, but they’ll be there just in general. So we can go down-

See All Episodes
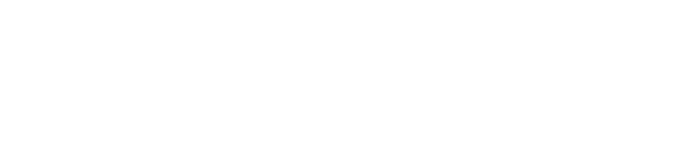
Schedule a 1-on-1 Consultation with a Formtek Technical Specialist:
Formtek is comprised of a family of long-established metal forming equipment manufacturing brands, each with a well-known name and a history of providing innovative and reliable equipment to the metal forming and metal processing industries. With seven brands spread across seven facilities, our network of personnel are here to support your range metal forming and fabricating equipment needs.
Looking to improve your productivity and profitability of your operation? Looking for a solution to address a particular application? Schedule a no obligation, 1-on-1 consultation with a Formtek Technical Specialist today and let us develop a customized solution to address the specific needs of your operation.
We're Here to help
Have questions about our machinery and equipment? Looking for a solution to address a particular application? Looking to improve the overall productivity and profitability of your operation? Please don't hesitate to reach out or schedule a no obligation, 1-on-1 consultation with a Formtek Technical Specialist — we'd love to help.